NTS Norma Hengelo
NTS Norma is a leader in precision machining and ultra-precision modules and can boast of achieving an accuracy of less than one-thousandth of a millimetre. However, the company was experiencing measurement deviations of small holes (less than 5mm) in Product X during the measurement process on a Coordinate Measuring Machine (CMM). The aim of this research is to identify the root cause of these measurement deviations and improve the manufacturing process of Product X. A DMAIC approach is used as a guideline to improve the efficiency and effectiveness of the manufacturing process.
In the Define phase, measurement deviations of small holes in Product X are identified. In the Measure and Analyse phase, measurements were conducted on Product X and test plates to determine the causes of the measurement deviations. Several causes were identified, including environmental temperatures, the anodising process, and the measurement strategy.
In the Improve and Control phase, possible solutions were proposed to address the identified causes of the measurement deviations. The proposed solutions included controlling the environmental temperature and standardising the measurement strategy for the measurement program and CMM tools. A step-by-step plan was developed to ensure that the measurement strategy was consistent across all measurement programs and CMM tools.
The improved manufacturing process can lead to increased efficiency and effectiveness, as well as a reduction in the number of defective parts produced
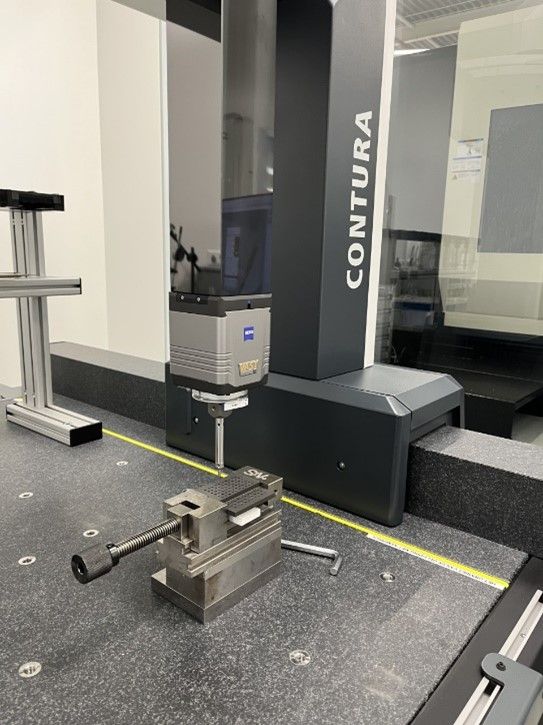
CMM measuring the test plates
Comments
Log in to read and post comments