Sanders Ijzergieterij en Machinefabriek B.V
MsC ME D&M Internship Twan Elferink
At Sanders IJzergieterij en Machinefabriek B.V. (Iron casting and engineering works) a new sprue design was tested, making use of the Exone 3D (binder jetting) printer. After discussing the literature researched, I was guided and given the resources to perform a full experiment. Sanders is a 177-year-old company founded in 1846. Because of this, combined with its reputation and impact on the region, Sanders received the royal title 'hofleverancier'. It started as a foundry but has also specialized in gear and machine parts manufacturing since 1918. It is currently located in Goor. In 2015 the ExOne 3D sand printer was added to the inventory for creating moulds. It prints (single-use) sand molds for casting, able to create highly detailed and complex shapes, up to sizes of 1800x 1000x700mm. It is used to create complete sand molds for casting. Recently, complex mold systems have been investigated, and now feasible and financially viable with this 3D printer. In my research, a novel and new sprue design concept was created and applied in practice, for a real set of Sanders products. These were further machined into final products at a customer company, which was also visited. A sprue is a vertical tube where the metal melt is poured into, before entering the mould core. The traditional straight sprue was replaced by a novel spiral sprue design, which has only been tested experimentally since 2019. Literature noted high improvements in flow properties, reducing entrainments, hence drastically reducing the porosity of castings. Porosity causes early failure of castings or even complete product rejection. An adapted design method for the spiral sprue concept was successfully applied at Sanders, including additional simplified modeling of the ceramic filter's influence on flow. The filling time was predicted accurately (error of 4% maximum) and confirmed the flow properties were according to the model and likely in optimal condition. Cutting and thorough post-processing showed no porosity and a good quality casting. Compared to the traditionally made castings of the same products, a significantly lower ferrite content was achieved, desirable for the product application. Hardness values remained similar between both casting types (traditional and 3D-printed). These material properties were investigated by a certified laboratory, to which casting cut-outs were delivered.
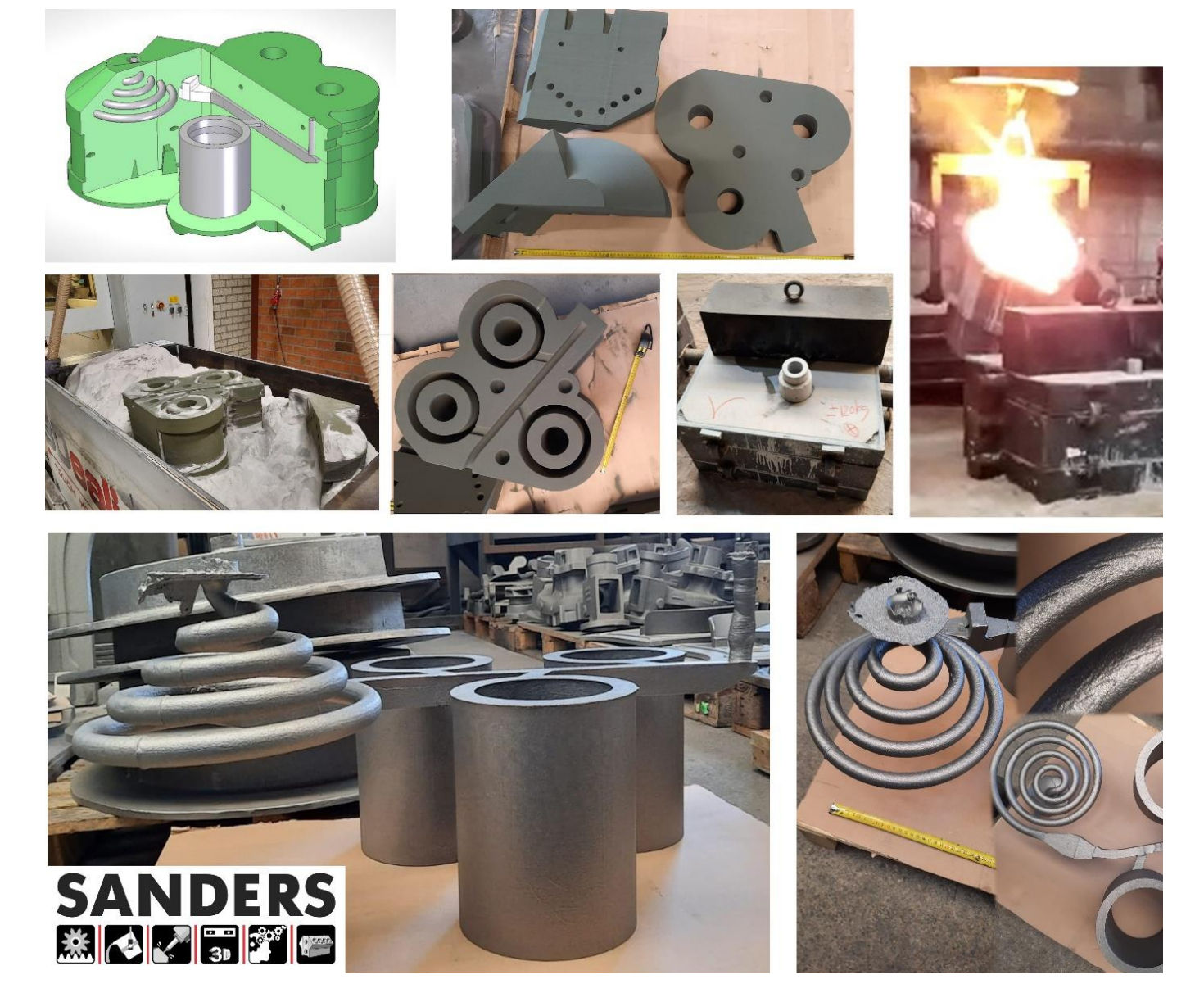
Comments
Log in to read and post comments